Guest Column: Next-shoring: A CEO’s guide
October 2014 Newsletter
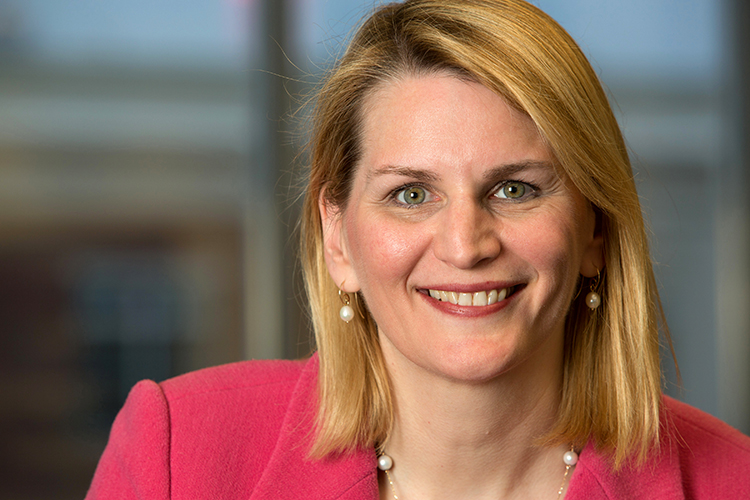
The importance of manufacturing to the American economy is undeniable. Economic development is crucial to supporting manufacturing communities (and vice versa), and the work many of you do to build infrastructure or develop the local workforce is contributing to the growth of manufacturing across the country. But manufacturing is changing, and its future looks nothing like its history. Rather than focus on offshoring or even “reshoring”—a term used to describe the return of manufacturing to developed markets as wages rise in emerging ones—today’s manufacturing strategies need to concentrate on what’s coming next. The synopsis below is adapted from “Next-shoring: A CEO’s guide,” an essay I wrote with Sree Ramaswamy and Lou Raseey for the McKinsey Quarterly, January 2014. Please visit for a full collection of content on the future of manufacturing. – Katy George
Katy George is a director in McKinsey’s New Jersey office; Sree Ramaswamy is a fellow of the McKinsey Global Institute and is based in the Washington, DC, office; and Lou Rassey is a principal in the Chicago office.
Evolving demand from new markets places a premium on the ability to adapt products to different regions. Meanwhile, emerging technologies that could disrupt costs and processes are making new supply ecosystems a differentiator. Accordingly, a next-shoring perspective emphasizes two forms of proximity: to demand and to innovation.
Economic fundamentals
The case for next-shoring starts with the economic fundamentals of demand (since the importance of local factors is growing) and supply (as the dynamics of labor and energy costs evolve).
Most demand is local. More than two-thirds of global manufacturing activity takes place in industries that tend to locate close to where their products are sold. This simple fact helps explain why manufacturing output and employment have recently risen, both in mature economies and in emerging markets such as China. Emerging markets’ share of global demand is also climbing, from roughly 40 percent in 2008 to an expected 66 percent by 2025. As that share rises, the diversity of needs it reflects leads to fragmentation: in the automobile industry, 90 percent of recent capital expenditures have involved product derivatives worldwide and capacity expansions in new markets.
Labor costs become less important... Rapid wage growth in China hasn’t choked off manufacturing expansion there. True, in a few labor-intensive, trade-oriented industries such as apparel, labor-cost changes often tip the balance in locating production. But higher wages in China are also increasing local demand, thus reinforcing manufacturers’ local-investment choices.
…and energy costs, too? In part because of lower natural-gas prices, the McKinsey Global Institute (MGI) estimates that by 2020, lower-cost energy could boost US GDP by $400 billion to $700 billion. And energy-storage technologies, especially lithium-ion batteries and fuel cells, are becoming more capable and less costly. As advances continue, more companies may be able to focus on local demand patterns rather than energy concerns in placing their geographic bets.
Technology disruption ahead
At the same time, advanced robotics, 3-D printers, and the large-scale digitization of operations are poised to alter fundamental assumptions about manufacturing costs and footprints.
Advanced robotics. Cheaper, more proficient robots are another reason companies may locate more manufacturing closer to major demand markets—both in developed countries and in developing nations, where robots could bridge shortages of some production skills. MGI research suggests that 15 to 25 percent of the tasks of industrial workers in developed countries and 5 to 15 percent of those in developing countries could be automated by 2025.
3-D printing. Cheaper 3-D printing is already allowing some companies to accelerate product development. Soon, targeted usage of in-house printers will enable new supply-chain models that, in some cases, may replace traditional parts suppliers. The equivalent of copy or print shops may emerge to manufacture items based on customers’ design specifications.
Digitized operations. Cloud computing, mobile communications, advanced analytics, and the Internet of Things—the growing collection of sensors and actuators embedded in products and equipment—are starting to combine in powerful ways. Increasingly, products can communicate: with each other, with robots and advanced machines inside factories, and with customers and suppliers. Manufacturers will get an unprecedented global view into who makes what, where, and how well, enabling some to buy and sell underused production lines “by the hour.”
Next-shoring
In developing and emerging markets alike, both proximity to demand and proximity to innovation will be critical. Next-shoring isn’t about the shift of manufacturing from one place to another but about adapting to, and preparing for, the changing nature of manufacturing everywhere.
Optimizing location decisions. New products, market segments, and consumer preferences are exacerbating perennial risks (such as variations in seasonal demand, wages, and exchange rates) to boost uncertainty. Operational agility—the ability to adapt design, production, and supply chains rapidly to fluctuating conditions while preserving economies of scale—will thus carry an even greater premium. Volkswagen, for example, has moved from traditional vehicle platforms to modular architectures that provide greater flexibility for manufacturing several product variants.
Building supplier ecosystems. New combinations of technical expertise and local domain knowledge will become the basis for powerful new product strategies relying on collaborative supplier ecosystems. More-robust information flows among partners will yield improvements ranging from surer logistics to better payment systems. Many manufacturers’ supply bases may thus need significant upgrades to create joint competencies in areas such as robotics.
Developing people and skills. All this will place a premium on manufacturing talent. Organizations will need to invest more in formal training and on-the-job coaching to bridge crucial gaps, such as too few technically skilled workers in advanced economies and too many workers experienced only in routine manufacturing in developing economies. The ability to build external relationships—with suppliers, education partners, and local-government officials who can influence the development of vibrant, sophisticated supply ecosystems—will be a major source of competitive advantage.
□ □ □
The new question for manufacturers won’t be whether to produce in one market for another, but how to tailor product strategies and match local needs with the latest manufacturing know-how and digital expertise. Accordingly, while the road map for every company, industry, and location will be different, we believe that the principles we’ve laid out here should be useful for all.
Copyright © 2014 McKinsey & Company. All rights reserved.